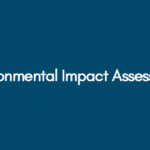
Environmental Impact Assessment
February 27, 2021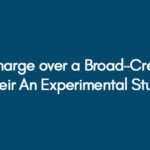
Discharge over a Broad-Crested Weir An Experimental Study
February 27, 2021Chapter – 1; Introduction
Research and development has played a vital role in the progression of the civil engineering construction industry. The last few decades has seen progressive adaptation of new methods of construction, which has resulted in more economical, environmentally friendly and stronger structures.
There are many materials that have been historically used for the construction of various structures such as homes and multi-story buildings. Some of the primary structural / building materials include concrete, which is a product of cement, stainless steel frames, composite piles and timber. The application of the materials depends upon the user requirements, structure design, site conditions and financial capacity.
The question then arises as to why the utilization of cement is considered to be much versatile in the development of civil structures?
Cement has been widely used to produce concrete for the last many centuries due its versatile usage and extensive flexibility. This product of cement can take any required shape and can be adopted for a variety of site conditions. Furthermore, it meets the local fire codes without any additional requirement of fireproofing treatments, and its reliability is considered to be better than its counterparts during natural or man-made disasters such as fire. This is because of its slower heat transfer rate characteristic, which resists the spread of fire. It is also known to have a higher thermal mass, which results in better thermal and acoustic properties (Swamy, 2008). Moreover, structures made from concrete are stiffer / stronger, reducing the chances of vibrations in the structures.
In the following chapters of this report, the fundamental questions such as “what is the composition of cement, how cement is produced, and where does the different types of cement are utilized?” will be discussed in detail.
Research aims
The following are the aims of this report;
- To analyze the composition of cement currently being produced around the world.
- Develop understanding of how its composition affects the civil engineering structures.
- Analyze the importance of latest developments in the production of cements and understand how the latest technology can be adapted to reduce the environmental concerns.
Research objectives
The following are the research objectives of this report;
- Identify the composition of cement.
- Identify how cement minerals impacts the properties of the cement and the consequent production of concrete.
- Review the recent research articles to identify how the variations in composition of cement affect the civil engineering structures.
- Review applications of the different cement types, with respect to their differences in compositions.
- Outline the standardized cement types.
- Suggest how to choose the right type/composition of cement.
Chapter – 2; Literature review
The production of cement can be categorized it into two main types, namely hydraulic and non-hydraulic cement (Deborah and Thomas, 2009). This characterization is based upon their ability to be used in water. The non-hydraulic cement needs dry conditions to be settled, and therefore it cannot be used in wet conditions. However hydraulic cement, for example Portland cement, which is normally used for the production of concrete, can be applied in a variety of conditions, and therefore this type of cement is the subject of this study.
The mixture of cement is fundamentally composed of activated aluminum silicates and silicate-based/siliceous materials. These additional materials in cement provide it with the strength to be applied in wet conditions and help it to avoid the attacks of aggressive chemicals (Zhang et al., 1999).
History of cement indicates that Romans manufactured cement by mixing volcanic ash (activated aluminum silicates) with slaked lime in order to make hydraulic cement. Fly ash, which is recovered from power stations for controlling pollution, is more economical as compared to volcanic ash, and it is being used as a pozzolans in manufacturing of hydraulic cement. After reviewing the research completed by Bye in 1999, Neville, in 2012, and Mehta & Monteiro in 2005, the basic composition of cement was determined, as detailed in the following section;
Composition of cement
The composition of cement allows it to get strengthened under wet conditions by getting harder. This strength of hydraulic cement is because of the reaction of hydrates which are not very soluble in water. Besides the various uses of cement, its most important use is as component in mortar production in masonry and of concrete. This combination makes it a strong and durable structural material (Neville, 2012).
Composition of hydraulic-cements (such as Portland cement) is a mixture of silicates and oxides, with the four primary components being C3S, C2S, C3A, and C4AF. The approximate details of the composition of cement are given below in Table 1;
Table 1; Basic composition of cement (Source: Mindess et al., 1996)
Name |
Formula |
Abbreviation |
% Composition |
Tricalcium Silicate (Alite) |
3CaOSiO2 |
C3S |
~55% |
Dicalcium Silicate(Belite) |
2CaOSiO2 |
C2S |
~15% |
Tricalcium Aluminate (Aluminate) |
3CaOAl2O3 |
C3A |
~10% |
Tetracalcium Aluminoferrite (Ferrite) |
4CaOAl2O3Fe2O3 |
C4AF |
~10% |
Calcium sulfate dehydrate / Calcium oxide (Gypsum and lime etc) |
CaOSO32H2O / CaO |
C H2 / C |
~10% |
Mechanical properties of cement depend upon the silicate content. The liquid phase during the process of kiln sintering (also know as firing) is achieved by the help of celite and brownmillerite. The chemistry of above mentioned reactions is not comprehensively explained and is still a research topic (Mindess and Young, 1981)
More than 90% of the Portland cement’s composition contains the four primary cement minerals, as shown in the table above. The other 10% consists of sulfates of calcium and alkali, CaO, MgO, and various other constituents in minor quantities which are residual of the clinkering and grinding processes (Taylor, 1997).
All four of these minerals play a distinct role in the cementing process (hydration). The C3S and the C2S are responsible for the properties of the C_S_H gel, known as calcium silicate hydrate, which is the primary hydration product. It is important to note at this point that C3S hydrates at better rate as compared to C2S, and therefore it is responsible for higher early strength. The C3A and C4AF also play a role in the hydration process; however these minerals do not contribute heavily in the properties of cement. Furthermore, calcium silicates cements are economically not possible to produce at high scales without the addition of C3A and C4AF components (Jennings and Thomas, 2009).
Chapter – 3; Methodology
The most common type of cement being used around the world for general purposes is the 'Ordinary Portland Cement', also referred as OPC. This cement is manufactured by a process known as calcination. In this process, limestone (calcium carbonate) is heated with other materials in required quantities in a kiln at a temperature of 1450 °C (Mehta and Monteiro, 2005).
Figure 1: the reaction process of cement (Source: Mehta and Monteiro, 2005)
Mechanism of calcinations indicates that a molecule of carbon dioxide is released from calcium carbonate, resulting in production of calcium oxide, commonly known as quick lime, which is then synthesized with other materials. This results in formation of a hard substance known as 'clinker'. Then it is grinded with a small amount of gypsum to produce cement. It is the basic component in the manufacturing of mortar, concrete and non-specialty grout. Portland cement is most commonly used in concrete production. Concrete is a complex material composed of aggregate (gravel and sand), cement and water. Keeping in view the constructional use of concrete, it can be molded into any desired shape to produce a structural (load bearing) element. Portland cement is available in two colors, grey and white (Jennings and Thomas, 2009).
This chapter will analyze the changes in compositions to produce various types of cements. This obviously can have influential impact on the development of civil engineering structures as change in compositions affects the structure design as well as the economy of the project. Therefore the methodology adopted in this report is to analyze different types of cements and their subsequent impacts. There are many types of cement, some of which have been presented the section below.
Variance methodology in cement production
Energetically modified cement is produced by the process of grinding, which contains dominant composition of pozzolanic minerals that have been treated using the primary milling process (Justnes and Ronin, 2013). This process results in a better replacement of Portland cement from economical, performance and reliability point of views. It yields more power/strength and also saves carbon dioxide (Robin et al., 1999). If improvements are not done then resulting concrete will have the same physical characteristics as ordinary concretes, at considerably lower costs (Justnes et al., 2005).
Portland blast furnace cement contains a large amount of ground pulverized slag which is almost 65-70%, whereas rest of its composition contains Portland clinker and gypsum. Due to large yield of slag sulfate, the surface resistance increases and heat evolution dwindles, besides the fact that these products yield high ultimate strength. Therefore it can be used instead of Portland sulfate-resisting cements (U.S. Federal Highway Administration, 2007).
Almost 30-35% of fly ash is present in Portland fly ash cement and because of pozzolanic’s nature of fly ash, the desired strength can be maintained. Since fly ash allows lower concrete water, it helps to achieve early strength and maintain it. Availability of quality fly ash at cheap prices will result in an economic substitute of ordinary Portland cement. Availability of volcanic ashes in countries such as Italy, Mexico, Chile, Philippines increased the production and demand of Portlad pozzolan cement (Detwiler et al., 1996).
Portland silica fume cement is also produced when silica fume is added in the composition of cement, which can offer particularly high strengths. Cements containing 5-20% of silica in their chemical composition are particularly produced. This inclusion of silica fumes in the composition to Portland cement in usually done at the concrete mixer (SFA, 2014).
Bricklaying mortars and stuccos are manufactured using masonry cements; however, it should not be used in concrete. Various complex materials are used as a remedy, composed of Portland clinker and many other ingredients including limestone, hydrated lime, water-proofers and cooling-agents (Van Oss, 2007).
To avoid the shrinkage problem in the structures which is commonly faced with hydraulic cements, expansive cements can be manufactured which contain expansive clinkers, such as sulfo-aluminate clinkers, in addition to Portland clinker. This helps in formation of large floor slabs (up to 65m square) to be prepared easily by avoiding contraction joints (Lukose, 2013).
In order to produce a fine quality of ground cements, mixtures of cement with sand, slag or other pozzolan type minerals are finely blended together. This increases surface area for various chemicals to react, despite the fact that such cements have the same characteristics as the other standard cement types. The comprehensive grinding process uses up to 50% less energy to fabricate this productas compared to other ordinary Portland cements (Justnes et al., 2005).
Pozzolan lime or Slag- lime cements are a mixture of lime and ground pozzolan or slag and lime. In ancient times it was used by Romans, and those structures are the proof of its strength. This cement takes time to develop its strength but their maximum strength is very high. The strength produced as a product of hydration process is the same, if not more than of those produced by Portland cement (ASTM D5370, 2014).
For the purpose of decoration, colored cements are also manufactured by adding pigments to Portland cement, which are generally prepared in the form of blended hydraulic cements (Detwiler et al., 1996). These types of cements are also known to enhance the sustainability; this will be discussed in the next chapter.
There are many more types of cements which are being produced through varying the composition of the cement, in accordance with the requirements of the civil structure and associated environmental as well other conditional parameters (Swamy, 2008). Therefore, it is important to further investigate the results these variations can produce and develop understanding on how the compositional variations can be standardized.
Chapter – 4; Results and discussion
From the research conducted in the previous sections, it has been observed that cement of distinct characteristics can be produced through adaptation of different production methods. This chapter will provide the standardized set of applications in the form of results, highlighting the key differences amongst mostly used cement types.
According the ASTM International (AASHTO M 85, 2009), The standardized general type of cement are; Type 1 –Ordinary Portland Cement (OPC), Type 2- Moderate Sulfate-Resistant, Type 3 – High Early Strength, Type 4 – Low Heat of Hydration, and Type 5 – High Sulfate Resistant. The Chemical compositions of all these types are invariably different, and the selection of the type is based upon the structural design requirements and site conditions.
Table 2; Basic composition of cement (Source: Mindess et al., 1996)
Type |
Characteristic |
C3S % |
C2S% |
C3A% |
C4AF % |
Fineness kg/m2 |
1 |
General purpose |
55 |
19 |
11 |
8 |
375 |
2 |
Moderate Sulfate and moderate heat |
51 |
23 |
6 |
12 |
375 |
3 |
High early strength |
56 |
19 |
11 |
8 |
545 |
4 |
Low heat |
27 |
48 |
4 |
11 |
385 |
5 |
High Sulfate resistant |
39 |
42 |
4 |
9 |
385 |
The application of the type-1 cement includes general construction such as roads, bridges, buildings, pavements, precast units and floors, as shown in the figure 2 below. It has fairly high content of C3S which ensures better early strength development (Jennings and Thomas, 2009)
.
Figure 2: type 1 general purpose cement structures (Source: Google images and about civil.org, 2014)
The utilization of the type 2 and 5 cements in the civil structures is given as below. Both of these types are similar in a way that these contain a very low C3A content. The type 2 cement is mostly used for structures which are expected to be exposed to soil or/and water containing sulfate ions (Detwiler et al., 1996).
Figure 3: type 2 and 5 cement structures (Source: aboutcivil.org and Google images, 2014)
The high sulfate resistant (type 5) cement is used where there is a definite requirement of resistance against reactive chemicals, primarily against higher levels of sulfate ions (ASTM (2008), as shown in the figure below;
Figure 4: type 5 cement structures (Source: aboutcivil.org and Google images, 2014)
It is important to note that the composition of the cement or cement type is not the only parameter that may concern the civil structure developments. Other design and construction practices, such as converting can also play a vital role in the durability and strength of the structure. Most importantly, the fundamental practiced must be followed and the basics of the construction process must be right. For example, during the converting process for any project, the water to cement ratio (w/c) is extremely important, as failing to achieve the optimum ration would result in an un-acceptable formation of the structure (Jennings and Thomas, 2009). This has been demonstrated as below;
Figure 5: the importance of construction practices (Source: aboutcivil.org and Google images, 2014)
The application of high early strength cement (type 3) is in infrastructure that is requires to be developed in shorter times and with cold weather concreting. This type of cement grounds more finely and has slightly more C3S content for high early strength. These include primary structures such as road and equipment foundations, as shown in the figure below;
Figure 6: type 3 cement applications (Source: aboutcivil.org and Google images, 2014)
The white colored cement is used where there is requirement of coloring the structure, example of which is shown in the figure below;
Figure 7: Use of white cement (Source: aboutcivil.org and Google images, 2014)
White Portland cements (WPC) are used on its own for the structure’s surface treatments. These are fundamentally used for the development of various architectural fixtures, terrazzo, sculptures, tiling, in chips and exterior cladding. White cements has lower contents of magnesium and iron, the elements which gives cement the grey color, however they do not contribute to the properties of cement. Hence, WPC is no different to the standard cement of the same type, except for their color. WPC are more expensive than the standard cement, and are more often used for research purposes too due to their high resolution results in NMR measurements (Jennings and Thomas, 2009).
The blended hydraulic cements have also been standardized in accordance with the ASTM international (AASHTO M 240, 2012). These standards suggest that blending supplementary components in the OPC improves the performance as well properties of the cement. This blending enables production of cement at a reduced cost; because various materials such as fly ash which is an industrial waste product are utilized in the production process.
It further enhances the environmental performance of cements as it acts as a sink to hazardous products. An example of this is the Portland limestone cement, which is produced through addition of 5 to 15% of limestone in standardized cement. This product has the ability to achieve the desired performance of concrete while ensuring sustainability improvements. This blended cement was introduced in the market in 2008 under the name of CSA A3001.
Another example is the Supersulfated cements. Its composition shows that it consist of 75-80% ground granulated blast furnace slag, 10-15% gypsum or anhydrite and a little Portland clinker as an activator. Production of ettringite develops their strength however strength growth is similar to that of Portland cement (BS EN 15743, 2010). Calcium aluminate is hydraulic cements composed of limestone and bauxite.
Clinkers such as ye’elimite helps in production of Calcium sulfo-aluminate. In result of hydration, ettringite is produced. Special physical properties (expansion or rapid reaction) are incorporated by adjusting the amount of available calcium and sulfate ions. Their ability of using less energy has raised their demand in China, where several million tones are being produced per annum (Bye, 1999; Zhang et al., 1999). The reason for low energy requirement is the lower kiln temperature required for reaction, and lesser required quantity of limestone. Use of less limestone decreases the amount of carbon dioxide liberated but rate of emission of sulfur dioxides are increased.
Manufacturing of cement at all stages produce various harmful effluents for environment in the form of smoke of dust, gases and noise, vibration of machinery and during blasting in quarries (Jennings and Thomas, 2009). Precautionary measures must be taken and designated equipment, such as dust collectors etc must be used excessively in order to overcome these drawbacks.
Chapter – 5; Conclusions and recommendations
It is the basic and most important need of any country to develop infrastructure which is enduring, efficient, reliable and effective. It is also important to keep economic point of view in mind while establishing a long lasting infrastructure. There is a disquieting situation for all of us whenobserving a crumbling infrastructure. If the construction industry wants to achieve durability in construction while keeping in mind the environmental conditions and threats, it would be important to emphasize on the development of best building materials.
Cement (in the form of concrete) has been considered to be one of the most durable and reliable construction materials. However, its composition selection in-terms of the right type of content hold prime importance for any civil structural development project. By manufacturing strong, sustainable and economically viable materials, one can ensure that the desired attributes are successfully attained in the civil engineering structures.
The research conducted in this report suggests that via ensuring optimum construction and design practices, and application of the right type of cement can produce durable and high strength infrastructures. The details of the required composition of cement, in accordance with requirements, can be attained form readily available resources. These resources have been developed through years of research and development, and it is absolutely vital to attain guidance from these resource in order to avoid and cracks, ageing and natural disasters.
Research is being completed to enhance the sustainability of cement, and the recent advances in the technology has helped in the development of new types of cement which are known to consume less energy in production and have a definite reduction in the release of toxins to the environment. Holistic Design helps us to anticipate a global methodology with respect to concrete and construction, through optimum material selection, comprehensive design, efficient development and trouble-free maintenance plans. In order to achieve durable performance, material as well as structural stability must be achieved.
References
- AASHTO M 85 (2009) ASTM C150 AND AASHTO M85 STANDARDS AND HARMONIZATION UPDATE [online]. Available from: http://cement.org/manufacture/pdf/AASHTO%20and%20ASTM%20standards%20and%20harmonization%20update%20for%20fall%202009%20MTC%20meeting.pdf. [Accessed 13 October 2014].
- AASHTO M 240 (2012) AASHTO M240 and ASTM C595. Portland-Limestone Cement.An option to improve sustainability [online]. Available from: http://www.cptechcenter.org/ncc/TTCC-NCC-documents/SP2012_Presentations_Reports/13%20Melander-AASHTO%20M240--ASTM%20C595.pdf. [Accessed 13 October 2014].
- ASTM (2008) Annual Book of ASTM Standards, Volume 4, published by the American Society for Testing and Materials.
- ASTM D5370, (2014). Standard Specification for Pozzolanic Blended Materials in Construction Applications
- BS EN 15743, (2010). Supersulfated cement. Composition, specifications and conformity criteria
- Bye, G.C. (1999) Portland cement: composition, production and properties.2nd. Thomas Telford. pp. 206–208.
- Deborah, N. H. and Thomas, D. E. (2009) A life-cycle assessment of Portland cement manufacturing: comparing the traditional process with alternative technologies. Journal of Cleaner Production, 17: 668–675.
- Detwiler, R.J., Bhatty, J.I. and Bhattacharja, S., (1996). Supplementary Cementing Materials for Use in Blended Cements, Portland Cement Association
- Jennings, H., Thomas, J. J. (2009). Materials of cement science primer. A final report submitted to the Infrastructure Technology Institute for TEA-21 funded projects designated A474 Northwestern University, Evanston. Available online from : http://www.iti.northwestern.edu/publications/utc/tea-21/FR-5-Jennings-Thomas.pdf [Accessed 13 October 2014
- Justnes, H. and Ronin, V. (2013) Performance of Energetically Modified Cement (EMC) and Energetically Modified Fly Ash (EMFA) as Pozzolan. SINTEF.[ online]. Available from: http://www.sintef.info/upload/Performance_of_energetically_modified_cement.pdf [Accessed 13 October 2014].
- Justnes, H., Elfgren, L. and Ronin, V. (2005) Mechanism for performance of energetically modified cement versus corresponding blended cement. Cement and Concrete Research.[online]. Available from: http://web.archive.org/web/20110710185446/http://www.emccement.com/Articles/EMC%20mechanism%20paper.pdf [Accessed 13 October 2014].
- Kosmatka, S.H. and Panarese, W.C. (1988) Design and Control of Concrete Mixtures. Skokie, IL, USA: Portland Cement Association. pp. 17, 42, 70, 184
- Lukose, R.M., (2013). Characterization of Portland Cements, Expansive cement and High-Alumina Cement, and their Variation in Properties with Different Components. Vol. 1, Issue: 6 ISSN: 2320-6586
- Mehta, P. and Monteiro, J. M. (2005) Concrete: Microstructure, Properties, and Materials. 3rd ed. McGraw-Hill Professional. Chapter 6.
- MIT (2009) Cement's basic molecular structure finally decoded [online] Available from: http://newsoffice.mit.edu/2009/cement-0909 [Accessed 13 October 2014].
- Mindess, S. and Young, J.F. (1981) Concrete. Englewood, NJ, USA: Prentice-Hall.
- Mindess, S., Young, J.F. and Darwin, D., (1996) 2nd Ed. Prentice Hall.
- Neville, A.M., (2012) Properties of Concrete. 5th ed. Trans-Atlantic Publications. Chapter 2.
- Ronin, V., Jonasson, J.E and Hedlund, H (1999) Ecologically effective performance Portland cement-based binders, proceedings in Sandefjord. Norway: Norsk Betongforening. pp. 1144–1153.
- SFA, 2014. Silica Fume Association, Fairfax, Virginia. Avalable online at: http://www.silicafume.org [Accessed 13 October 2014].
- Swamy, R. N. (2008) Sustainable Concrete for the 21st Century Concept of Strength through Durability. Japan Society of Civil Engineers Concrete Committee Newsletter, 13.
- Swamy, R. N., (1998) Design for chloride contaminated harsh environments: concrete protection the key to durable service life. The Arabian Journal for Science and Engineering, (23) 2C: 3-40.
- Taylor, H.F.W. (1997) Cement Chemistry.2nd Ed. London: Thomas Telford.
- Van Oss, (2007) Minerals Yearbook, Cement - USGS. Available online at: http://minerals.usgs.gov/minerals/pubs/commodity/cement/myb1-2007-cemen.pdf [Accessed 15 October 2014].
- S. Federal Highway Administration (2007) Ground Granulated Blast-Furnace Slag. [online]. Available from: http://www.fhwa.dot.gov/infrastructure/materialsgrp/ggbfs.htm [Accessed 13 October 2014].
- Zhang, L., Su M. and Wang Y.,(1999) Development of the use of sulfo- and ferroaluminate cements in China in Adv. Cem. Res. 11 N°1, pp. 15–21
Get 3+ Free Dissertation Topics within 24 hours?