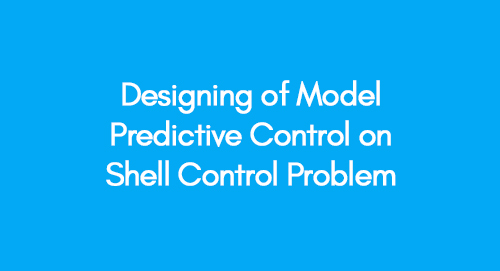
Operations Management
February 27, 2021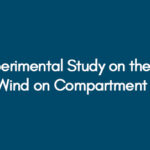
An Experimental Study on the Effect of Wind on Compartment Fire
February 27, 2021Building Information Modeling (BIM) exemplifies efficient construction analyses, fostering collaboration, minimizing errors, and optimizing resource allocation for cost-effective and timely project execution. In the dynamic world of construction, where every moment counts, and accuracy is non-negotiable, Building Information Modeling (BIM) emerges as a revolutionary force. It introduces a new age of efficiency, transforming the traditional landscape of construction practices. As the heartbeat of this transformation, BIM transcends beyond a mere technological tool; it becomes the linchpin that connects various facets of construction analyses seamlessly. In this blog, we explore the pivotal role played by BIM in reshaping project management, fostering collaboration, and optimizing construction processes for unparalleled precision.
Use of Building Information Modeling (BIM) in Construction Industry
Efficient Construction Analyses, underpinned by the capabilities of BIM, redefine how projects are conceived and executed. Gone are the days of disjointed efforts and fragmented communication. BIM is a digital nexus, bringing architects, engineers, contractors, and stakeholders onto a unified platform. This collaborative approach ensures that everyone involved in the project works with the same up-to-date information, significantly reducing the likelihood of errors and miscommunications. The result is a streamlined, interconnected workflow that saves valuable time and sets a new standard for accuracy and efficiency in the construction industry.
Introduction
Figure 1: Building Information Modeling Standard (Source: NIBS, 2006)
While recent computer-aided technologies have significantly enhanced various aspects of facilities and engineering, their effective utilization hinges on collaborative and integrated planning at the project's inception. Effective planning can mitigate process fragmentations, improving project quality and subsequent decision-making.
The impact of these processes on parameters such as supply chain management, workflow sequence, and data accuracy is substantial. Applying such tools in the project aims to eliminate conflicts between design and engineering, ultimately reducing project timelines by eliminating the need for rework. The system provides real-time information during on-site work, enhancing the infrastructure's life cycle management.
-
Research Aim
The primary objectives of this research are as follows:
-
Investigate and comprehend the contribution of Building Information Modeling (BIM) to efficient construction.
-
Identify and emphasize the diverse techniques and resources available to maximize the effectiveness of BIM applications.
-
Determine whether BIM represents the ultimate solution for enhancing the efficiency of construction and development.
-
Research Objectives
-
Research Questions
Literature Review
BIM technology has long been a presence in the construction industry, evolving with the introduction of various programs, software, and applications that have given rise to different systems. These systems, known by various names and acronyms such as Building Information Modeling (BIM), VC 3D CAD (Virtual Construction, 3 Dimensional AutoCAD), IS (Information System), CIC (Computer Information Construction), and IT (Information Technology), have collectively contributed to the creation of an integrated and interactive space for information sharing.
Jung and Gibson (1999) define Computer Information Construction (CIC) as an integration spanning the entire life cycle of a project involving computer systems, management, information technology, and corporate strategy. CIC is recognized as an enabler, particularly for efficient project management and engineering and construction processes.
Information Systems (IS), as noted by Jung and Gibson (1999), were initially developed for labour-intensive tasks but have evolved to be deeply integrated into business procedures, supporting and transforming corporate strategy. Another recent development, a form of BIM called a computer-integrated system, is currently a subject of discussion regarding its benefits and associated costs.
Aranda-Mena et al. (2008) emphasize that BIM serves various purposes for different corporations, ranging from a software application to documenting and designing built information to advancing business options that necessitate the implementation of contracts and policies among stakeholders. Given the interactive nature of BIM, the opinions and perspectives of various stakeholders, including contractors, engineers, and others, hold significant weight for effective and efficient implementation.
The term "BIM" has been defined in various ways, contributing to confusion regarding its potential benefits. The Business Value of BIM report (McGraw Hill, 2009) describes BIM as a procedure for creating and using digital models for construction and business operations. Woo et al. (2010) view BIM as an intelligent 3D model utilizing virtual building information to optimize the building model, reduce risk, and enhance the project's value. Zuppa et al. (2009) highlight BIM as a tool for coordination and visualization in the Architecture, Engineering, and Construction (AEC) sector, aiding in error prevention.
The National BIM Standard (2006) defines BIM as a digital representation of building factors, aiming to be a reliable forum for decision-making and an interactive knowledge-sharing platform throughout the project's life. The diverse definitions underscore the challenge of quantifying potential benefits and defining BIM, with stakeholders holding different perceptions of what constitutes benefits.
The construction industry, a key contributor to the UK economy, has achieved competitive advantages in areas like low-carbon products, architecture, and engineering. The industry plays a vital role in achieving climate change targets set by the UK government. The government's significant role in public sector procurement, responsible for over 30% of projects, emphasizes the importance of the construction industry in renewing and expanding the UK's infrastructure.
The capability assessment presented aims to analyze the construction industry's current state and outline future opportunities for integrating BIM into the sector. BIM, seen as a collaborative tool, combines design, creation, and maintenance concepts for effective resource and information utilization throughout a project's life.
BIM has gained global recognition as a game-changing phenomenon in the Information and Communication Technology (ICT) sector. Countries worldwide are developing their infrastructure and capabilities to implement BIM, viewing it as a collaborative measure between the software and construction industries. Through reports like the one published by BIS in 2011, the UK government has embedded BIM in public procurement projects to enhance efficiency. The construction industry in the UK has responded positively to this initiative, establishing the country as a leader in the global implementation and exploitation of BIM-driven technology, contributing to economic growth nationally and internationally (BIM, 2011).
Methodology
-
The Lean Concepts and Principles
Before analyzing how BIM can be approached and used to enhance the performance of any construction project, it is important to shed light on the lean concepts that have been used for many decades to streamline construction strategies. We must remember that the lean concept is still young and advancing steadily. New concepts arise, and the substance of the old ones changes, yet the following methodologies are still being used in the subject industry:
Just-in-time approach: Any action that includes cost without increasing the worth is considered waste. It might be because materials are being moved unnecessarily, accumulating an abundance of stock, or the utilization of faulty production methods, making reworking the created products necessary. The JIT concept helps in enhancing the benefits and profit on investments by decreasing levels of stock, enhancing item quality, lessening variability, decreasing production and lead times of delivery and reducing different expenses; for example, those connected with machine set-up and breakdown of equipment (Koskela, 2010).
Exploring BIM in Design Coordination Along With Integrated Project Delivery
They attempted to keep everybody as occupied as possible to boost production efficiency. This brought about expansive inventories, a long time for production, high rates of defective items produced, outdated items, delivery plans getting hard to meet, and hence high expenses. All of these could have been avoided by adopting “just in time” (JIT) manufacturing.
3-D and 4-D Modeling to Improve Production Methods: Basic for all phases in the building construction procedures is the broad/extensive utilization of information technology. The 3D model depends upon offering a shared database that supports providing the latest drawings and data accessible from the database to all distinctive teams in the development process. Various documentation might then be prepared from this database, such as distinctive 2D and 3D presentations, materials specifications, and drawings for assembling and production. The database can also process information for calculating costs, time planning, and the critical information required for the customer and the future lodger.
The 3D-modelled design concentrates on the outline of the building, spatial planning and development, the utilization of materials, and various other aspects. The 3D model is a static model built to represent the physical building in the computer. This could be seen as a detriment to the development (construction) process since the methodology is dynamic and requires a dynamic presentation (GSA, 2007).
4D-CAD is an integral model that integrates an object-oriented 3D-CAD model with the fourth dimension in the form of time. 4D-CAD is a form of data visualization that is simpler to comprehend than the conventional methodologies, for example; 2D drawings and time plans, which are utilized to oversee development projects. 4D-CAD is a method for envisioning a construction based on logic.
The utilization of visualization and the adoption of the 4D concept empower the project partner to concentrate on the significant data and other resources. Using 4D tools gives more opportunities to carry out related predictions and more proficiently assess the design, construction scheduling or constructability. Along these lines, the design and development stages will be extensively integrated, creating a more effective development process.
The 4D idea, by visualization of the development procedure, is a productive tool for planning to organize the logistics of the site throughout the planning stage rather than during the production/construction stage. The site layout might be visualized and simulated with a 4D CAD tool for the project participants, which will help the site designer organize the exercises, material streamlining and site logistics. 3D-4D modelling benefits stakeholders, engineers, architects and contractors (Liston et al., 2000).
Total Quality Control (TQC): TQC is an administration tool for enhancing overall performance. Quality development began with investigating raw materials and items utilizing statistics-based systems. In Japan, quality development has developed from just the inspection of items to total quality control products. The term total being used here refers to three extensions (Shingo, 1988):
- Extending quality control from production to all branches of the company.
- We are extending the thought of quality to all operations in the organization.
- Extending quality control from the workers to the administration.
The quality strategies have been created and grown in correspondence with assessing the idea of quality. The main idea has transformed from an investigation perspective (sampling theory) through process control (procedure control involving statistics and the seven other tools) to persistent process change (the new seven devices) and, at present, to designing quality into the item and methodology (quality function deployment).
Total Productivity Maintenance: Total productivity maintenance (TPM) is the self-sufficient maintenance of production hardware by small groups of operators with different skills (Nakajima, 1988). Total productivity maintenance expands generation yield by keeping up perfect working conditions. The production operators are there to perform routine maintenance undertakings regularly, while technical experts and engineers handle more specific assignments. TPM system aims to avoid maintenance (using such designs or choice of simple equipment), upgrades on equipment, and preventive and predictive maintenance.
Employee Involvement: The involvement of employees is critical for working in any organization. Quick response to any issue that occurs obliges the strengthening of the employees. Non-stop betterment is intensely subject to the normal perception and motivation of the workforce and, subsequently, the thought of quality circles. Keeping in mind the end goal to avoid waste connected with the division of work, teams of multi-skilled or self-directed groups have been created for projects/ production/client-based production.
Continuous Improvement: The key thought behind this concept is to uphold and enhance the working gauges through continuous enhancements. It's an endless procedure. A continuous improvement procedure includes everybody from the precise lowest part to the top, which is essential because little periodic enhancements lead to a huge positive change over the long haul. (Koskela, 1992).
Time-based Competition: Compressing time around the association to achieve competitive benefit is considered time-based. This is the summed-up manifestation of just-in-time theory (JIT logic). As per Ohno, shortening time is advantageous, for example, by decreasing the work not identified with processing, abatement in the stock, and simplifying identifying the problem (Robinson, 1991). Time-based competition has gotten prevalent, particularly in managerial and data work where the JIT theory sounds unfamiliar.
Concurrent Engineering: Concurrent engineering is related to the project's design phase period; even though it's dependent upon ideas similar to JIT and TQC, it didn't evolve specifically from them. The term Concurrent alludes to an enhanced design process by upfront requirements analysis, consolidating the limitations of consequent stages into the conceptual stage, and tightening of change control at the close of the design phase.
Value-Based Strategy: This strategy alludes to "conceptualized and articulated value as the reason for contending" (Carothers and Adams 1991). Firms driven by value-based systems strategies are client-oriented rather than contender-oriented firms. Continuously improving client value is one fundamental quality of value-based management.
Visual Management: An inclination towards visual control in generation, quality, and work environment planning is what visual management is about. This is one of the first JIT thoughts, and the objective is to render the standard which has to be applied, and a deviation from it is instantly conspicuous by anyone.
Re-engineering: Re-engineering alludes to the radical arrangement of processes and undertakings, particularly concerning the usage of information technology. Consistent with Hammer (1990), distinguishing and splitting far from antiquated standards and basic assumptions are the key problems in re-engineering.
-
BIM Performance Assessment & Application; Case Study
Many BIM applications help effectively execute the strategies described in the previous section. For instance, BIM encourages early error identification and collisions, subsequently helping accomplish high quality. Thus, BIM helps in total quality control. An alternate example is that BIM encourages co-ordination, which thus prompts the participation of employees.
It is interesting that BIM likewise supports accomplishing many of these principles. For instance, reduction of the period of the project by discovering clashes in the early stages of the design phase by lessening non-value-adding activities and increasing the value of the client. A case study has been presented in this section to show that applications of BIM aid in accomplishing many such key lean principles.
A typical case study of constructing a multi-storey building can be used to show that BIM can be successfully used in all the project's construction stages and how it can impact the project's life cycle. For any multi-storey building, various activities must be listed to develop an understanding of the project requirements to complete the structure of the building.
In this assessment, the client is looking forward to developing a 6-storey residential tower, for which the major activities (till completion of building structure) can be listed below;
Table 1; Project Activities
Project’s Major Activities |
|
Activity 1: Design and Planning Outlining the requirements of the client/residents, completing the geographical analyses, subject soil analyses, site-layout planning, calculations and drawings, and building layout plans. |
|
Activity 2: Approvals Proposing the completed documentation from activity 1 to clients, carrying out discussions and amendments and preparing the final approved documentation/designs/plans, etc
|
|
Activity 3: Project Handling/Management Completing the BOQs (bill of quantities), establishing the procurement team, completing arrangements for tender approvals, and selecting the team of workers/builders/construction team. Prepare the primary site per the approved documentation, import the required machinery, and set up/develop workshops. |
|
Activity 4: Basement and foundations development Initial and complete the excavation process to construct the foundations and basement according to approved plans. |
|
Activity 5: Material of construction The complete selection process of material construction, procurement, and construction material assembling. |
|
Activity 6: Structural works Complete the structural installation works based on the material section decisions from Activity 6 and all other associated engineering works. |
|
Activity 7: Testing and finishing Complete finishing of structural and engineering work, complete the testing procedures, and complete flooring, roofing and walling works. |
As described in Table 1 above, the successful completion of all activities requires the implementation of the optimum project completion methodology. Previously, we have discussed how lean principles can support completing such activities, and the following shows how BIM can be effectively utilized in this case study.
-
Design Activities of the Multistory Building
In addition to providing a 2D model, a BIM-generated 3D model will be developed to enhance support in visualizing the project. This tool can support presenting the proposed models to clients and other stakeholders, as shown in the figure below.
Figure 2: BIM Design and Implementation (source: Facilities, Princeton University 2014)
Through the application of BIM modelling tools, as shown in the figure above, the building design/model can be thoroughly examined, and the design team can perform simulations and benchmark the performance quickly. There is better correspondence and comprehension from 3D visualization (McGraw Hill Construction, 2009).
Various issues associated with all the project activities can be settled promptly during the design phase. Subsequently, there will be fewer issues in the plans following and, henceforth, fewer errors (McGraw Hill Construction, 2009). Any design updates completed to the building could be immediately updated. Henceforth, less revision will be required because of conceivable errors or omissions in the drawing (Eastman, 2008).
The application of BIM in this project is expected to allow all the workers to participate at an early stage and work simultaneously on all aspects and activities of the project. This provision reduces the time taken for design and decreases possible errors and omissions. This also helps decrease the cost as the value engineering process is initiated simultaneously and not at the end of the design phase (Eastman, 2008).
BIM generates 3D visualizations and quantifies material amounts. This aids in exact and expense assessment at an early stage. Henceforth, the configuration plan of a building can be checked/verified qualitatively and quantitatively at an early stage in the process (Eastman, 2008). If any updates are completed in the model, it can be promptly redesigned, and henceforth, a completely reliable drawing might be created when design adjustments are made.
-
Construction Activities of the Proposed Multistory Building
The 3D design parameters in the model will be interfaced with the development plan and subsequently will be conceivable to show how the building and the site might look at any instance. This is an attractive tool which is being utilized in this project. Troubleshooting is another parameter rated as the top means managers save time and cash utilizing BIM (McGraw Hill Construction, 2009). In 2-D drawings, any modifications in one drawing are not upgraded in other related drawings. This prompts numerous conflicts and consequently generates error inputs. Many of these conflicts are discovered after the work has begun at the site, which may prompt numerous site clashes, legitimate questions and revision requests.
Better comprehension and easier understanding of life cycle costs and environmental performance can also be performed using the subject system (Azhar et al., 2008). At any design phase, the BIM can get the bill of quantities for tender approvals and generations and estimate the cost of materials for selection purposes. These qualities will be utilized to get more reliable expense estimation early in the process.
Architectural sustainability is considered one of the primary factors when designing and constructing any complex. Various regulations have been applied at the governmental level to complete the project by using sustainable practices. Through the use of BIM, the building model can be integrated with the energy modelling tools. This is to assess energy utilization and henceforth furnish a chance to construct this multistory building with better energy effectiveness. The overall sustainability of the building will be improved through efficient utilization of materials, waste reduction, better performance of the materials and equipment, and many other factors.
Impact of BIM & LCA in Improving Resilience and Sustainability in Construction Projects
The downstream process of constructing a multi-storey building can utilize the digital item information and be used for manufacturing structural frameworks (Azhar et al., 2008). In BIM, the components are currently characterized in 3D; subsequently, their automated creation utilizing numerical control apparatus is encouraged. This encourages exact off-site fabrication and subsequently lessens expense and development time. The probability of on-site updates occurring is decreased. Afterwards, larger segments/parts could be manufactured without worrying about later conceivable measurements being changed because other components were developed (Eastman, 2008). The site is likewise more secure since many components are getting manufactured off-site and trucked to the site, keeping onsite exchanges the least (Smith, 2007). This also ensures that there is less amount of waste generated on-site, which enhances the sustainability score of the project
The application of BIM in this case study is expected to furnish a great source of data for all the different systems utilized as a part of the building, which can used to check if all of them are in order and functioning as the building is finished/completed (Eastman, 2008). Likewise, the data about maintenance and warranty of mechanical parts, control systems and others could be delivered and, therefore, help improve facility management.
-
BIM Benefits and its Applications; Case Study Analyses
The advantages that come with the use of BIM have real effects on quality control, completing tasks on time, production rate, overall expenditure, project economics and safety (Superman, 2007), as shown in the figure below;
Figure 3: BIM planning and constructability analyses (source: REVIT BIM, 2007)
The BIM model used for this project will be obtained from one of the various BIM service providers, such as REVIT, Innovaya, Archi-CAD, and Saneo. The model to be used/applied in this project will be integrated with Primavera and/or MS Project to enhance the engineering performance during the project. Automated generation of project activities will establish clear goals for the workers/builders periodically in real-time. With recent optimizations in the BIM in terms of dimensions (time, cost, and life-cycle, discussed in detail in the next chapter), the construction activities presented in Table 1 can be completed with much enhanced efficiency.
Consistent with the survey led by McGraw-Hill developments, more than 48% of the owners say that the overall project proves beneficial, as not many RFI's and field coordination issues/problems occurred. BIM helps exchange data effortlessly, which is considered one of the prime benefits of its use. It usually produces better-quality data and can be reused (Azhar et al., 2008). Furthermore, BIM rapidly responds to plan or site issues (Eastman, 2008), eventually saving time and the project's cost. Some of the other benefits of BIM currently recognized are detailed below (Azhar et al. 2008), which can also be useful during the complete life cycle of the proposed building in this case study.
- Fabrication and other Drawings/Models: BIM can easily generate shop drawings as soon as the model's completion occurs. An example of this can be shop drawings made of sheet metal ductwork.
- Coding Reviews: Government bodies such as the rescue department and others use the BIM drawings codes to review building projects.
- Hazard Analyses: BIM can illustrate the possible failures graphically in the building, for example, evacuation plans, leaks, and other such failures, which holds a pivotal role in the engineering works
- Facility and Engineering Management: Space renovations/developments, maintenance and planning operations can be performed using BIM.
Figure 4: Operational methodology of BIM (source: Arayici et al., 2011)
-
Challenges/Barriers to Adapting BIM
From the research completed in this paper, it has been observed that the BIM is a valuable tool for the construction business. But it is not impeccable, and it is even now developing. There are still numerous tests and restraints in BIM that it must overcome.
Many questions are yet to be answered concerning the application of BIM, such as: who claims the rights of a model? Legal concerns display tests regarding who claims the ownership of the various designs, fabrication and development datasets, who makes payment for these, and who is answerable for their precision (Eastman, 2008).
The ownership of the data management responsibility is another aspect that needs to be answered. Furthermore, engineering firms frequently may not utilize BIM software, which prompts general contractors to outsource the whole model. This is tedious as well as expensive. Additionally, if people working on the same project utilized more than one type of modelling software, teaming up with them could be challenging and may cause a few data losses (Eastman, 2008).
Implementing BIM requires thorough comprehension and a plan before the change can start (Eastman, 2008).
Findings
This section synthesizes the analyses of the literature presented earlier and the completed case study. It delves into the key points, discussing details and providing relevant insights to fulfil the paper's objectives.
The amalgamation of various ideas, innovations, and processes discussed in this section showcases their significant impact on operations within the construction industry. These processes and activities are interrelated and mutually reinforcing, paving the way for their implementation as standard operating procedures by government agencies and major corporations. The overarching goal is to ensure the low-cost, high-quality sustainability of projects. However, achieving these transformations and collaborations necessitates the active involvement of major stakeholders, including government agencies, corporations, contractors, architects, sub-contractors, and researchers.
To enhance competitiveness and productivity quality in the UK construction industry, a proactive approach is suggested to implement necessary changes. Researchers have emphasized that individual quality of life is intricately tied to the products provided by the construction industry, ranging from houses and bridges to water and sewer lines, roads, airports, hospitals, and shopping centres. The construction industry's role in providing essential infrastructure, such as shelter, water, and power, is crucial for supporting connectivity, mobility, and commerce in the United Kingdom.
The construction industry contributes significantly to the country's gross domestic product and is a major job provider. The national economy's robustness is closely tied to quantifiable construction values, affecting the final consumer property prices. Business productivity in construction can further enhance the national economy by renewing existing bridges and infrastructure and adopting green products. Prioritizing efforts to modify structural designs and recycle materials is essential for ensuring green productivity and sustainability. This, in turn, minimizes the greenhouse effect and controls carbon emissions.
Despite ongoing debates about the construction industry's status, with conflicting views on whether it is improving or declining, there is a consensus that there is ample room for improvement. Analysts differ in their assessments, with some noting a continuous decline over the past thirty years, while others see significant improvements, such as advancements in pipe laying. Regardless of the perspectives, both parties agree that considerable enhancements are possible. Some key areas for improvement include:
-
Improvements along with BIM
Tulacz and Armistead, 2007, point out that studies that have documented construction efficiency in contrast to construction productivity show that 25 to 50% of waste is accounted for in managing, modifying and moving labour and machinery. The main key point highlighted in the report is that the advancement of technology can not only improve the efficiency of the construction industry but also look into meeting various other challenges faced by the nation, such as environmental sustainability. The research completed, and the detailed case study showed various interrelated activities, which, if implemented, will result in a breakthrough in productivity within the construction industry. The paragraphs below include a brief discussion of each of the activities.
Enhanced efficiency on the job site through effective interaction between machinery, people, information and processes. This is a dynamic set-up since the construction site is where equipment, people and equipment interact with each other to complete the tasks. To manage all these activities, utilising the available resources efficiently is imperative. Poorly managed resources can waste resources and time since the equipment will have to be moved multiple times, schedules will be mismanaged, and the workers will have to wait for the tools and equipment.
Use of BIM in Quantity Surveying Practice
The use of enhanced technology such as automated equipment (pipe installation and concrete movers), information technologies such as trackers, digital assistants, real-time movements and improvements in the process could lead to a great cut down in the waste and enhance the security and quality of the employees as well as the operations. The sequence of planning and segmentation proves to be obstacles in using such technologies. Furthermore, it is pertinent to state that efficiency within the job process and operations requires a skilled labour force adept at communication and collaboration and proficient in management and technological faculties.
Enhanced prefabrication, modularization, preassembly, off-site processes and fabrication should be implemented. These involve assembling or fabricating components and systems in manufacturing and off-site areas. Once complete, the equipment is shipped to the construction area for installation procedures. Implementing these techniques will bring about a lower cost, efficient utilization of resources, including labour and enhanced quality. Various barriers, including building codes, conventional designs, and procedures, hinder the use of such modern automated technologies.
Demonstration installation should also be implemented, including field experiments, seminars, training, and high-tech scientific laboratories that use reporting protocols and standardised testing procedures. Demonstration installation can be implemented to test the validity of new technology, procedures, and their impact on construction site implementation. If implemented effectively, they can reduce risk and mitigate innovation of contractors, engineers and subcontractors.
To support innovation, effective performance measures should be implemented, enabling innovation and ensuring corrective actions throughout the operation of the Project. This leads to an analysis by the organization about the success and failure of the project, the drawback or inefficiency of the Project, and any potential outcome of the Project. Given the nature of the construction projects and the industry sector, leading performance indicators are mandatory at all levels and Projects, respectively.
-
Prefabrication, Preassembly & Modular Construction
Various other factors contribute to work inefficiency on the job site, including exposure to high dust levels, noise, and extreme weather conditions, leading to inevitable fatigue. New technologies can lead to a lesser workload for the workers and ensure their safety since the equipment is easier to control and use. Also, altering the use of material can reduce the material's weight, making it easier to move and handle. Manufacture of building equipment away from the job site entails not only precision but also quality of the equipment. Pre-fabrication, modularization, pre-assembly and off-site fabrication all involve assembling or fabricating systems and equipment at offsite plants and manufacturing areas. When this is complete and the appropriate time comes, this equipment is shipped to the installation site. All these activities can be completed through the effective use of learning principles and with the application of BIM.
A survey was conducted to analyse the relationship between material technology and the subsequent productivity within the construction industry, based on a hundred specific construction-related tasks and found that:
- The use of lighter materials increased labour productivity by 30%.
- Labour productivity was also seen to increase when equipment and materials that can easily be installed or fabricated were used (Goodrum et al., 2009)
-
Resource Efficiency
Environmental impacts that arise from construction and demolition are astonishing. Landfill sites are one of the major sources of pollution since all the construction and manufacturing debris is brought to them every year. The Environmental Protection Agency has highlighted statistics about the magnitude and impact of construction and demolition, which owners, contractors, and designers can positively utilize.
On the other hand, modular construction efficiently utilises resources since it allows repetitive units to be reassembled within a controlled condition. Another factor to consider is the utilization of material waste, which results from conventional construction practices and weather intrusions. If finished before installation onto the construction site, whole modular units would lead to significantly less waste generation. Modular construction is based on moving a product in a controlled and tight condition towards project schedules. Considering the various site constraints, it would be an efficient tool for minimising the impact on the site, given the environmental concerns.
A report produced by the United Kingdom Waste and Resources Action Program states that off-site manufacturing can significantly reduce the amount of waste generated while ensuring quality cost predictability and enhancing the safety of the workers on site via the utilization of effective management tools such as BIM. Various industries within the construction sphere contribute significantly to the amount of waste generated; however, the mainstream ones include plasterboard, with up to 36% of waste generation; timber, with up to 25%; and packaging, with up to 5%. It is stated that up to 90% of waste can be reduced, including cement, timbre, concrete, pallets, cardboard, etc., by implementing the modern equipment used for construction and ensuring off-site manufacturing, for which much support can be obtained through the utilization of BIM and/or lean principles as detailed in the previous chapter.
-
Streamlined Construction Process
Four inherent stages comprise the construction process in the factory. First and foremost, approval of the design by the authorities and the end consumer; second, assembling module components within a controlled environment; third, transporting the equipment modules to the final site; and fourth, erection and assembling of modules to make a finished building, the final product, as shown in table 1 of chapter 3 A factor which is unique to modular construction is that both the assembling of modules as well site work is being conducted simultaneously. This has various benefits, including reduced construction time, increased efficiency, reduced finances and supervision costs, and an earlier occupancy permit. All the procedures are conducted within time and amalgamate as a part of the construction process.
Another factor unique to modular construction is that various constructions, including floors, roofs, walls, ceilings, and rafters, can be completed simultaneously. In comparison, when construction is done on-site, the ceilings cannot be built until the walls have been built; similarly, walls can’t be erected unless the floors are in place. Meanwhile, in modular construction, all walls, rafters, ceilings, and floors are built at the same time, and after their completion, they are brought to the site to be given the form of a building. The time taken in modular is half that consumed with conventional construction methods and techniques.
-
What are the Government and Industry Doing Already?
Since we have already seen how the use of BIM can effectively enhance the performance of a construction project (from the case study), it is, therefore, important to develop an understanding of the strategies the government is keen to adopt to benefit from this modular construction and project handling tool.
Given the widespread adoption of BIM technology within the construction industry, it is estimated that the United Kingdom government would save up to two billion pounds, according to the study conducted into the Business Case for Interoperable Building Information Modelling by Wix and Nisbet, 2008, which works well with a budget cut scheme that has been implemented by the government with the aim of fifteen to 20% savings on each of the Projects by next year. The implementation of BIM technology within the United Kingdom began in 2011 and has since become widely used in private and public sector organizations to procure and deliver product Projects. The BIS BIM Strategy lists down the drivers for BIM technology. It highlights three requirements that the construction industry and the government have implemented: (1) To achieve higher efficiency in operations along with reducing the costs of the assets; (2) Ensure efficiency and effectiveness of construction supply chains; and (3) basing the growth ambitions on a sector which implements forward-thinking approach.
The government has been working in continuous amalgamation with the construction industry council to ensure the implementation of BIM. There are various industry-focused programs which aim to implement the BIM technology, with a specific focus on the supply chain to give effect to the mandate of the government to ensure that all publically procured projects are delivered using the BIM technology by the year 2016 (Department for Business Innovation & Skills, 2014).
Throughout all levels of the supply chain, the use and implementation of BIM ensure transparency and collaboration between suppliers, engineers, and other stakeholders, which has inherently proven to be one of the greatest competitive advantages of BIM. It furthermore reduces waste produced through procurement, processing and materials. Furthermore, the key driver in the success of BIM is the benefit that the technology has created for clients, customers and all the stakeholders within the entire supply chain.
BIM has become recognized as a driver for competition and growth within European countries. The European Union Sustainable Construction Strategy aims to enhance the performance of the industries within their domestic sphere through BIM and ensure their competitive advantage in the global market. On the other hand, the application of BIM is currently being viewed by the European Union Directive on Procurement, and both the United Kingdom and the European Union must collaborate to ensure that any future protocols on BIM are compatible with the BIM technology already implemented within the United Kingdom.
The ICT industry within the United Kingdom is very advanced and modern, which can be an advantage for the United Kingdom. Therefore, it can provide a backbone for future developments and improvements within the BIM technology, which may be implemented within the United Kingdom. The BIS BIM strategy also pointed this out and was introduced internally by the software teams and construction markets.
Government Construction Strategy formulated the BIM technologies alliance, collectively representing BIM technologies and software(s). The main aim of the BIM technologies alliance is to collaborate with the government to ensure the effective embedding of existing BIM technologies and implement and develop future products and data analysis schemes to ensure effective and efficient protocol and procedural systems.
Engagement and collaboration between construction, manufacturers and products represent about 40% of the value of the construction industry within the United Kingdom, and manufacturers, more importantly, are the inherent contributors to the construction industry. The ability and willingness of the manufacturers to implement BIM data analysis and then provide feedback about their products is critical to not just the success of BIM technology but also for the future embedment of data throughout the lifecycle of the Project from the beginning to operations to the end product. The Construction Product Association has been actively involved in using BIM technologies. It has been involved in coordination between the product manufacturers to ensure good quality sustainably. Various standards, including SMART, IFC and COBie, have been implemented and collaborated with organizations, including the British Standards Institute, to produce an era of structured protocols (HM Government, 2012).
The final stage, the handover, is extremely important in ensuring that the product is produced and used as it was designed. It also ensures that it continues sustainable production with the same design. This area has been subject to observation by the Government's construction strategy and is implemented in public procurement projects through government soft landings. The synergy between the data provided by the BIM and the handover procedure, which involves analysis of the performance of the Project post its operation stage, is extremely strong. The BIM technology has successfully provided an approach to the industry that shifts the focus from supply chain operations to product post-operation and delivery analysis. Government soft landing has been enshrined within the BIM task group to ensure an efficient transition from construction/manufacture to operation/delivery of the product asset.
Industries throughout the globe have recognized the potential benefits of using BIM technologies and have immersed themselves in research for the same. An example is BCO, British Council of Offices, in collaboration with HOK Architects and Salford University, was successful in establishing a programme whereby knowledge-based benefits of BIM can be identified and then subsequently applied throughout the design, operation and manufacture of the Project (Department for Business Innovation & Skills, 2014).
Local and central governments have utilized procurement portals to ensure the effective delivery of the said product; however, the progress of BIM can be impeded if these portals react slowly to the data provided by BIM technology.
Undoubtedly, we have recognized the potential of BIM technologies and, therefore, have further developed digitally built Britain, which will give basis to our intention of becoming the global leader in BIM technology. Through digitally built Britain, the United Kingdom will not only support but also deliver the integration of BIM into various public procurement projects, including Smartcities. Using the BIM strategy will allow the investors and other stakeholders to ensure strategic alliances and sustainable investment decisions for those systems and Projects that cut throughout the city. One of the key objectives of digitally built Britain is to integrate various networks and software to work together while increasing the variety of BIM technological applications but decreasing their complexity. On the other hand, it is also important to develop the legal, political and commercial practices to support the use of BIM technologies.
-
The Recent Advancement in BIM
Throughout the previous two decades, the BIM made a critical movement forward. BIM extended its borders, getting extra functions (dimensions) and creating further opportunities in the construction industry. Initially, BIM transformed from a 3D-CAD configuration (including dimensions of shape, place and size) to a more efficient 4D configuration. The 4D BIM system added the fourth dimension of time to the three fundamental dimensions. This fourth dimension supports the full development coordination in design. According to the research conducted by Akinci et al. (2002), the BIM's 4D integrated tool can empower a contractor/subcontractor concerning materials requirements, human resource planning, layout planning, and supplies requirements in real time.
Thereafter, cost size was added to 4D concepts, which matured BIM to an advanced 5D level. The 5th dimension extension assures that it is conceivable to count the total expense for the development project and assumes that it is vital for project parts. The aggregate expense of project-related activities depends upon the data, such as the expense of labour, materials, and others that could be set up physically or consequently at the site with the assistance of chosen software tools.
The latest improvement made to BIM brought it to the new 6D level. The 6th dimension is related to the life cycle of the project, administration of site offices, and natural effect. Although some experts and scientists still believe that the 6th extension is under development, it is challenging to tide it into one entire framework, with the remaining five extents utilizing the software tools accessible in the commercial sector right now (GSA 2007).
Throughout the last decade, the imperativeness of BIM has been generally distinguished far and wide. In a few nations, BIM usage has gotten the backing of these states' administrations. The heading nations are the USA, Hong Kong, Australia, Denmark, Finland, Norway, Singapore, and the UK. The national frameworks related to BIM in the nations above are designed with state authorities in mind.
The General Service Administration (GSA) of the United States focused on a key and incremental method of adopting 3D, 4D and BIM technology. The current stage for GSA in BIM usage is investigating the utilization of BIM innovation all around the project's life-cycle in the following fields: validation of spatial project, 4D phase establishments, sustainability and power/energy consumptions, laser scanning, circulation and security approval, and various other building components. The United States is assuming the leading role in BIM usage, and this U.S. experience could be generally utilized by different nations (NIBS 2007).
The National Institute of Building Sciences of the United States developed and distributed the first National BIM Standard in 2007, which incorporated classifications, guidelines, specifications, and suggested practices. The building-SMART International Alliance for Interoperability (IAI) is an alternate organisation developed for BIM usage. IAI has united the partnered associations in 14 nations around the world. IAI formulated three standards, and the International Standards Organization (ISO) recognized these. BuildingSMART standards are created universally and spread information about facilities and projects, standard methods and standard names for items and properties (BuildingSMART, 2014). The following shows the operational model for these standards;
Figure 5: The BIM operational Model (source: self-edited)
Research conducted by Teicholz in 2004 pointed to the significant causes for the lack of advancement in the construction productivity field. This differentiates the project's design from its construction phase, which prompts a rise in the field costs. It mostly implies an inadequate consideration of the knowledge of construction throughout the design stage. It often prompts more changes and clashes throughout the construction stage, affecting the project regarding unwanted/additional delays and expenses.
Despite the construction industry’s adoption of Information Technology (IT) on a large scale, these applications/activities, for the most part, tend to run in a standalone mode that does not allow enhanced integrated efforts by the project team. This results in increased effort and time and reduces the capacity of the project team to react rapidly and successfully to changes in site conditions, scope, delays, and so forth. In this way, regardless of the wide execution of IT, it has not been able to produce considerable enhancements in the construction field.
The industry has countless small stakeholders, for example, customers, suppliers, designers, vendors, and contractors, who are regularly not in a position to lead in adopting new technology and practices, generally due to the insignificant size of these stakeholders.
There is a low level of investment in research and development in the construction industry. Therefore, new methods that are being developed are mostly constrained to individual projects only. This prompts a slower rate of adoption of new technology. The usage of BIM provides stakeholders with the best chances to make positive progressions throughout the design and construction phases of a project, which ought to enhance the gainfulness of construction sites (Suermann et al., 2007)
This research provides a platform to move the entire BIM methodology forward and expands on the paramount work embraced by the government and the industry's stakeholders. BIM activities are intended to provide a competitive advantage over conventional methods. It stretches the overall competencies and markets, from infrastructure investment and expert services to construction and ongoing asset administration. It also gives customers abundant new information regarding the built infrastructure and management tools.
Figure 6 below shows how the effort in design can influence the overall effectiveness of the project.
Figure 6: relation between level of effort in design and distribution of add-on values (Source: NIBS 2007)
These results show conclusive evidence that adaptation of traditional and/or BIM can save costs and improve the efficiency of the project.
Conclusion
From the research completed in this paper, it can be concluded that for the processes in the construction industry, efficiency enhancements and innovation are considered to be at the heart of the strategy and planning. Various methods can be utilized to achieve efficient construction and constructability, some of which have been successfully implemented throughout the UK. Along with such proactive, efficient methodologies, the BIM has gained much success among the major contractors in the construction industry, and it has been further supported at the governmental level, as the major stakeholders have identified this advancement as the key to success shortly.
Regardless of the technological advancements and their adaptations, the fundamental work ethics and practices can never be ignored. Following the basic principles in any project's designing, planning, construction, and finishing stages involve critical activities requiring optimising and utilising standardized working procedures. Attaining an optimum balance between the cultural and technical platforms is fundamental. Consideration of optimized site layout planning, sustainable material selection, efficient designing, an adaptation of most suitable construction techniques, construction activity planning, managed plan executions, communications system usage, troubleshooting, quality control, waste management, etc., are some of the most utilized approaches used to enhance the effectiveness/efficiency of any project.
Recent advancements in the field of digital engineering have revolutionized the construction industry. It is also worth noting that BIM technology provides state-of-the-art computer-aided models, supports generating insight knowledge in various steps, and produces a foundation for sustainable and efficient solutions. Besides the standard use of BIM in geometrical and data analyses, it can also be applied in cost analyses, which eventually benefit the building/infrastructure over its complete lifetime.
Furthermore, the application of this technology has produced fruitful results in the form of enhanced construction process productivity, end-product quality improvements and reduced associated impact costs. It further promotes higher levels of collaboration and an informed decision-making process with integrated associated project teams, forecasting the activities and chain of supplies to achieve the project's objectives. Moreover, it has been considered an effective communicational tool, which acts as the bridge between the project life and the client’s requirements in the form of a virtual world.
It is clear then that the quality and standard of life of the residents and the economy depend upon the government's and related authorities' capacity to provide various services, digital or otherwise, to people, static or moving. There is a need to predict the demand and supply of such products and digital services so that the authorities or organizations can match such demand and inform the customers in case of any discrepancy. BIM is one of the key drivers for data and networking, but it does so through connecting with various building blocks, which may include location data taken from mobile cellular services. Inherently, consumers want these services to be available when they want them. Therefore, it is necessary to carefully integrate different data sets with different data sources to ensure effective transformation in the paradigm of data volume.
BIM has revolutionised how the current industry thinks and operates, opening new efficiencies for the clients, supply chain management and project management. BIM is central to the integrator philosophy, guaranteeing the best value at each project life cycle phase. The government's construction strategy supports integrated supply chains. The industry now intends to accept that the evolved construction strategy and its BIM necessities will affect all parts of the supply chain and envoy a new era where organized in-house data about the assets under construction will encourage astute choice-making and ideal asset performance.
References
- Aranda-Mena, G., Crawford, J., Chevez, A., and Froese, T. (2008). Building information modelling demystified: does it make business sense to adopt BIM? CIB W78 2008 International Conference on Information Technology in Construction
- Arayici, Y., Coates, P., Koskela, L., Kagioglou, M., Usher C., and O’Reilly, K., (2011). BIM Adoption and Implementation for Architectural Practices. Available online at: <http://www.espncricinfo.com/world-t20/engine/match/716535.html> [Retrieved on 06 March 2014]
- Akinci, B., Fisher, M., Kunz, J. (2002). Automated Generation of Work Spaced Required by Construction Activities. Journal of Construction and Management. 128, No. 4
- Azhar, S., Hein, M., And Sketo, B., (2008). “Building Information Modeling: Benefits, Risks And Challenges”, Proceedings Of The 44th Asc National Conference
- Becerik-Gerber, B., Rice, S. (2010). The perceived value of building information modelling in the U.S. building industries, AECBytes, Retrieved from: http://www.itcon.org/2010/15.
- Best, R.,(2002). Design & Construction – Building IN Value., Oxford, Taylor & Francis
- BIM, (2011). A report for the Government Construction Client Group Building Information Modelling (BIM) Working Party, Strategy Paper. Available online at: http://www.bimtaskgroup.org/wp-content/uploads/2012/03/BIS-BIM-strategy-Report.pdf [Retrieved on 08 March 2014]
- BuildingSMART, (2014). International Alliance for Interoperability. Available online at: www.buildingsmart.com [Retrieved on 07 March 2014].
- Carothers, G.H., & Adams, M., (1991). Competitive Advantage through Customer Value: The Role of Value-Based Strategies.
- Department for Business Innovation & Skills, (2014). Available online at: <https://www.gov.uk/government/organisations/department-for-business-innovation-skills> [Retrieved on 02 March 2014]
- Deutsch, R., 2011. BIM and Integrated Design: Strategies for Architectural Practice, Somerset, NJ, USA, Wiley Publishing Inc.
- Eastman, C. 2011. BIM Handbook; A Guide to Building Information Modelling, Abington, Taylor & Francis
- Eastman, C.M., Sacks, R., (2008). Relative Productivity In The Aec Industries In The United States For On-Site And Off-Site Activities: Doi:10.1061/(Asce)0733-9364(2008)134:7(517)
- Facilities, Princeton University, (2014). How Building Information Modeling (BIM) Improves the Design and Construction Process. Available online at: http://www.princeton.edu/facilities/info/news/archive/?id=8217 [Retrieved on 01 April 2014].
- Government Construction Strategy, 2011. A One Year Report and Action Plan Update. Cabinet Office, Government Construction Strategy. Cabinet Office, 2011
- GSA (2007). GSA Building Information Modelling Guide Series.
- Hardin, B. 2009. BIM and Construction Management, Canada, Wiley Publishing Inc.
- HM Government, (2012). Industrial strategy: government and industry in partnership, Building Information Modelling. The document is also available from www.bis.gov.uk and URN 12/1327 [Retrieved on 01 March 2014].
- Holroyd T, (2003). Buildability: Successful construction from Concept to Completion.
- Hammer, Michael. 1990. Reengineering Work: Don’t Automate, Obliterate. Harvard Business ReviewM, London, Thomas Telford Pub.
- Jung, Y. and Gibson G. E. Jr., (1999). Planning for computer integrated Journal of Computing in Civil Engineering, ASCE 13, 4.
- Kocatürk, T., 2009. Distributed Intelligence in Design, Chichester, John Wiley & Sons Ltd.
- Koskela, L., (1992). Application Of The New Production Philosophy To Construction, Cife Technical Report 72
- Koskela, L., Arayici, Y., Coates, P., Kagioglou, M., Usher, C., Reilly, K.O., (2010). Technology Adoption In The Bim Implementation For Lean Architectural Practice.
- Lee, G., Sacks, R., and Eastman, C. M. (2006). Specifying parametric building object behaviour (BOB) for a building information modelling system.
- Liston, K., Fischer M. and Kunz, J. (2000), Designing and Evaluating Visualization Techniques for Construction Planning, Stanford University
- Liu, X. and Akinci, B. (2009). “Requirements and Evaluation of Standards for Integration of Sensor Data with Building Information Models.” Proc. of the ASCE Computing in Civil Engineering Conference, Technical Council on Computing and Information Technology of ASCE
- McGraw Hill. (2009). The business value of BIM: getting to the bottom line. Retrieved from: http://www.bim.construction.com/research/
- (2006). What is the NBIMS? Retrieved from: http://cic.vtt.fi/projects/vbenet/data/What_is_the_NBIMS.pdf
- NIBS (2006). Update on the National Building Information Modelling Standard. Proceeding on The 3rd National Congress on Digital Collaboration in the Building Industry.
- NIBS (2007). Change We Must.Proceeding on McGraw-Hill Change Conference.
- Potts, K. 2008. Construction Cost Management, Learning from case studies, Abingdon, Taylor & Francis
- Pacheco, F. 2007. Eco-Efficient Construction & Building Materials., University of Minho, Springer London
- Robinson, Alan (ed.). 1991. Continuous Improvement in Operations. Productivity, Cambridge
- REVIT BIM, (2007). BIM and Project Planning, Autodesk. Available online from: http://www.consortech.com/bim2/documents/BIM_project_planning_EN.pdf [Retrieved on 01 April 2014]
- Smith, D., (2007). AIA: An Introduction To Building Information Modeling (Bim), Journal Of Building Information Modeling
- Shingo, S., (1988). Non-Stock Production, Productivity Press, Cambridge
- Suermann, P.C., Raja, M., Issa, R.A., (2007). Journal Of Building Information Modeling.
- Teicholz, P. (2004).Labor Productivity Declines in the Construction Industry: Causes and Remedies. AEC bytes Viewpoint. Issue 4.
- Towey D., (2013). Cost Management of Construction Projects, Chichester, John Wiley & Sons Ltd.
- Tulacz and Armistead (2007). Advancing the Competitiveness and Efficiency of the U.S. Construction Industry. The National Academic Press
- Wix, J. And Nisbet, N., (2008). Study into the Business Case for Interoperable Building Information Modelling
- Woo, J., Wilsmann, J., and Kang, D. (2010). Use of as-built building information modelling. Construction Research Congress
- Zuppa, D., Raja, R., Issa, A., and Suermann, P.C. (2009). BIM’s impact on the success measures of construction projects, Computing in Civil Engineering
Get 3+ Free Dissertation Topics within 24 hours?