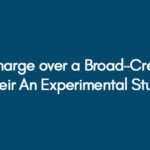
Discharge over a Broad-Crested Weir An Experimental Study
February 27, 2021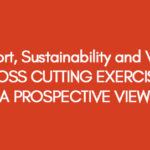
Transport, Sustainability and Visions CROSS CUTTING EXERCISE; A PROSPECTIVE VIEW
February 27, 2021The integration of Lean tools in cigarette production, including methods like value stream mapping and continuous improvement, is recognized in the literature for its effectiveness in enhancing efficiency, reducing waste, and promoting sustainable practices.
In today's dynamic manufacturing environment, the strategic adoption of Lean tools and techniques has become imperative for industries striving to bolster efficiency and minimize waste. This literature review delves into the specific domain of cigarette production, shedding light on how Lean principles orchestrate transformative changes. As a comprehensive strategy, Lean methodologies address inefficiencies and introduce a paradigm shift in an industry laden with unique challenges.
In the intricate landscape of cigarette manufacturing, Lean tools, such as Value Stream Mapping and Continuous Improvement, are instrumental in reshaping processes. The focus on visualizing and optimizing the entire production stream through tools like Value Stream Mapping provides manufacturers with actionable insights, leading to streamlined workflows and reduced timelines. Embracing the philosophy of continuous improvement ensures that the industry remains adaptive and responsive to changing demands. This review underscores the pivotal role of Lean principles in navigating the complexities of cigarette production, paving the way for heightened efficiency and sustainable practices in the tobacco manufacturing sector.
The following text comprises the introduction of the study.
Introduction
This paper explores a comprehensive analysis of diverse lean production strategies designed to improve the performance of manufacturing industries. This research aims to delve into various papers, articles, and journals authored by different specialists in different manufacturing sectors to gain a comprehensive understanding of lean principles and techniques.
Following a thorough investigation of lean manufacturing techniques, the researcher aims to assess the successful implementation of these tools in cigarette manufacturing. Consequently, the cigarette production process will also be scrutinized to ascertain how lean principles can be effectively employed to enhance the overall performance of the cigarette production industry.
Literature Review
Over the past few decades, numerous research publications have extensively documented the application of lean manufacturing across various industrial sectors. Originating in the West in the early 1990s, lean production gained momentum. It was notably featured in the book "The Machine that Changed the World" (Womack, 1990), showcasing lean methods pioneered by leading global auto manufacturers.
The appeal of lean production is rooted in observational evidence suggesting its capacity to enhance organizational competitiveness (Lowe, 1997; Oliver, 1996). Central to lean manufacturing is eliminating seven types of waste, ensuring optimal use of materials in production. Research by Shah and Ward 2007 indicated that reducing waste through lean principles can significantly enhance organizational efficiency, encompassing production effluents, time losses, inefficient resource utilization, and other forms of waste.
The primary objective of implementing lean production practices is to improve overall productivity while reducing lead time and costs (Karlsson and Ahlstrom, 1996). Quality management plays a crucial role in lean manufacturing, as poor quality management increases waste in human and material resources. Implementing quality management at the right time is seen as optimizing manufacturing process control (Nakamura et al., 1998). Noteworthy companies like Toyota, Pratt and Whitney, Ford, Sikorsky, Delphi, and others have achieved substantial savings by adopting lean manufacturing processes (Schmidt, 2000). Lean manufacturing can be implemented through key elements critical for its success.
In a competitive business environment, lean practices offer various opportunities for manufacturing industries to meet customer demands with high quality and on time. Additionally, lean production fosters employee skills development through education and multi-skilling initiatives.
Examining the application of various lean tools adopted by different manufacturing industries, it is essential to acknowledge that the lean concept is continually evolving. New concepts emerge through research and development, as well as practical experience, replacing previous practices. However, Total Quality Control (TQC) and Just in Time (JIT) remain the most widely used lean tools in the manufacturing industry, with several other concepts stemming from these techniques.
Organizations that embrace lean manufacturing within their operations can significantly improve their operational performance, which is tailored to suit their specific business needs (Ferdousi and Ahmed, 2009). Organizations must first identify the value stream map to implement lean thinking, a crucial step in recognizing production systems aligned with a lean vision. Value Stream Mapping (VSM) has found application in various manufacturing industries (McDonald et al., 2002). Workflow across the value stream should minimize Non-Value Added Activities (NVAA) to reduce wait time, moving time, queuing time, setup time, and other delays (Pattanaik and Sharma, 2009).
In addition to TQC and JIT, manufacturing industries have adopted various other lean tools, including 3-D and 4-D Modeling, Total Productivity Maintenance (TPM), Employee Involvement, Continuous Improvement, Time-based Competition, Concurrent Engineering, Value-Based Strategy, Visual Management, Re-engineering, and other techniques, all playing vital roles in the development of manufacturing industries.
Despite many publications on lean implementation, few have addressed the cigarette manufacturing industry. This industry faces significant pressure globally due to recent legislative revisions, increased competition from multinational industries, and the advent of e-cigarettes. The subsequent section analyzes the application of these tools to assess how their utilization can substantially support the performance enhancement of the cigarette manufacturing industry.
To better understand how lean tools and techniques can be integrated into the cigarette manufacturing industry, it is crucial to delineate the fundamental processes involved in cigarette production.
Cigarette Manufacturing Process
The production of cigarettes involves two primary processes: primary processing and cigarette manufacturing. The majority of wastewater generated in these processes is attributed to primary processing. In contrast, the cigarette manufacturing phase produces minimal to negligible amounts of wastewater.
Primary Processing
The stage of processing tobacco takes place before the production of cigarettes. The figure below outlines the fundamental step of this process;
Figure 1: Primary Tobacco processing (source: EPA, 2006)
The tobacco obtained from various sources, including local, offshore, and reconstituted, passes through conditioning cylinders, where steam is added to moisten and loosen the tobacco. The tobacco which has been conditioned is sent to storehouses, where blending is performed. Various tobacco blends are seasoned in barrels, dried, and then moisturized. Any local "Burley" tobacco utilized as a part of the mix is processed independently (flavour is added, and it is dried) before the last round of blending. The last tobacco mix is cut, dried, and re-moisturized. The tobacco is then directed to flavouring chambers for final flavouring. The prepared tobacco is sent to storehouses and the cigarette assembly processes.
Cigarette producers also include low-density tobacco, also called expanded tobacco, in their blends amid the last steps of the tobacco primary processing stage. The tobacco is exposed to carbon dioxide gas and conditioned such that the carbon dioxide becomes solid inside the tobacco. The solidified tobacco is warmed quickly, releasing carbon dioxide vapour. As the vaporization occurs, the tobacco cells grow, making tobacco with a low density.
Cigarette producers mix the flavours, representing their tastes in the diverse brands of cigarettes. Flavourings are produced in the form of batches. The different elements for the diverse flavours are blended in tanks and pumped to the flavour chambers utilized for primary processing. Once in a while, flavor-blending tanks are washed out, which creates wastewater. These wastewaters are released along with other primary processing waste streams, and they constitute a small fraction of the wastewater created and released during the entire manufacturing process.
Manufacturing Process
Cigarette makers use tobacco from the operations in the primary processing to produce cigarettes. The figure below portrays the accompanying steps by and large included in the cigarette manufacturing:
Figure 2: Cigarette Manufacturing Stage (Source: EPA, 2006)
The blended tobacco, which may incorporate reconstituted, expanded, and different assortments of tobacco, is passed on from the primary processing storage to the machines in cigarette production. The cigarette-producing equipment inserts the tobacco onto the cigarette paper as one rod before pasting the paper around the tobacco and slicing the rods to the right length for the cigarettes. The containers that hold the glue from the cigarette-producing machines are exhausted intermittently and washed with boiling water.
The cigarette-producing machines then place filters between two cut cigarettes, attach the filters to the cigarettes using filter paper, and slice the filters to make two cigarettes. The equipment downstream of the process performs the packaging of the cigarettes.
Waste Management
The various types of wastewater produced in different processes are documented in descending order of volume:
Process of Reconstituted Tobacco: This includes excess water for dilution from the sheet forming process, surplus concentrated tobacco extracts, steam condensate from installed evaporators, blow-down from air contamination control equipment and evaporators, machinery runoff, and floor washing water.
Primary Processing: Some process chambers (e.g., flavouring chambers) employ rotoclone hydrostatic precipitators for air contamination control. These rotoclones purify the air by capturing dust in water, releasing the resulting water-dust slurry as a blow-down stream. This constitutes the primary portion of the wastewater generated in primary processing. Waste is also generated during operations for treating wastewater at direct dischargers.
The treatment of wastewater for tobacco products at direct production centres generally involves biological treatment with nutrient removal, known as BNR. The key steps in the BNR treatment process include:
- Primary clarifiers
- BNR wastewater treatment (comprising activated sludge, phosphorus removal, nitrification, and de-nitrification)
- Secondary clarifiers
- Dewatering of sludge(s) from clarifiers
- Post clarifiers
Application of Lean Practices in Cigarette Manufacturing
Due to the increased expectations of customers and worldwide competition, industries attempt to expand productivity at lower costs and to deliver the best products and services. Under these conditions, it is important to actualize lean manufacturing systems to enhance the process environment with sensible investment. The concept of JIT can be introduced, enabling the cigarette manufacturing industry to enhance the benefits and profit on investments through a decrease in stock levels, improvements in product quality, reduction in variability, decrease in production as well as lead-times of delivery, and consequently enforce a reduction in various expenses, primarily which associated with machine setups and equipment breakdown (Koskela, 2010).
Even though the complete success of applying lean thinking, in the long run, relies on a good understanding between the administration and on-site workforce, viable administrative information systems are needed to instil proper organizational values and lean programs such as “Continues Improvement”. If these management standards are coordinated with available resources, this lean system can be incorporated effectively to achieve higher yields. Specifically, the possibility of turning the batch process into one continuous process can be investigated while reviewing the primary process. Other processes, such as material handling and blending, can also be reviewed, considering the state-of-the-art efficient technologies that can be used to improve the overall process of manufacturing cigarettes. In short, in light of the continuous improvement techniques, each block of the process can be reviewed, and possible alternatives can be recommended, which may prove to be more effective in the longer run of the organization.
The TQC, an administration tool for enhancing overall performance, can also be applied in cigarette manufacturing. The quality development plan will undertake investigations of raw materials while utilizing systems based on statistics. In Japan, the quality development initiative undertook a plan that went from mere inspection of items/materials to total quality control of products (Shingo, 1988). The quality enhancement plan can be extended from raw materials in the primary process to the end product of the cigarette.
Accordingly, future studies can be carried out on supply chain administration to attain good control, consistent performance and reliability. Moreover, the lean procedure related to Total Productivity Maintenance (TPM) can also be applied in the manufacturing of cigarettes. The TPM is an insufficient maintenance of facility equipment, ensuring optimum working conditions at all times for production. The optimum utilization of resources is also applied to waste treatment procedures and waste reduction.
Therefore, it can be concluded that adopting lean techniques can enable the cigarette manufacturing industry to improve its production efficiency. The improvement is expected to have a positive influence on the overall business of the organization in terms of the reduction of all forms of waste. Considering the long-term objectives, continuous improvements through adopting lean principles will generate positive results for the cigarette manufacturing industry.
Conclusion
The literature review underscores the potential benefits of applying lean tools and techniques in cigarette production. The analysis highlights the adaptability of lean principles, particularly Total Quality Control and Just in Time, showcasing their potential to enhance efficiency and reduce costs. The identified wastewater sources in production processes indicate opportunities for waste reduction through lean practices. Despite industry-specific challenges, the review suggests that adopting lean thinking can significantly improve operational performance and environmental sustainability in the cigarette manufacturing sector. Embracing lean methodologies emerges as a strategic imperative amid evolving regulatory landscapes and increased competition.
References
- EPA, (2006). Final Engineering Report: Tobacco Products Processing Detailed Study 821-R-06-017
- Farooquie, J.A. and Mohapatra, A.B., (2009). Japanese Manufacturing Techniques and Practices: An Indian Perspective. Jordan Journal of Mechanical and Industrial Engineering, pp. 175-180
- Ferdousi, F. and Ahmed, A., (2009). An Investigation of Manufacturing Performance Improvement through Lean Production: A Study on Bangladeshi Garment Firms, International Journal of Business Management, vol 4(9), pp. 107-115
- Kapuge, A.M. and Smith, M., (2007). Management Practices and Performance Reporting in the Sri Lankan Apparel Sector. Managerial Auditing Journal, 22 (3), pp. 302-319.
- Karlsson, C. and Ahlstrom, P., (1996). Assessing changes towards lean production. International Journal of Operation & Production Management, pp. 25-42.
- Koskela, L., Arayici, Y., Coates, P., Kagioglou, M., Usher, C., Reilly, K.O., (2010). Technology Adoption In The Bim Implementation For Lean Architectural Practice
- Lowe .J., (1997). High-performance manufacturing evidence from the automotive components industry. Organization Studies, Vol. 18 No. 5, pp. 782-798.
- Mercado, G., (2007). Question Garments: Ask the Lean Manufacturing Experts to Apply Lean in the Garment.
- Mc Donald. J, Van Aken E.M, Rentes. A.F., (2002). Utilizing simulation to enhance VSM: A manufacturing case application. Int I logist Res Appl 5(2): 2(3-232).
- Nakamura, M., Sakakibara, S. and Schroeder, R., (1998). Adoption of Just-In-Time manufacturing methods at US and Japanese Owned Plants: some empirical evidence. IEEE Transactions on Engineering Management, pp. 231-239.
- N., (1996). Lean production practices international comparisons in the auto component industry. British Journal of Management, vol.7 special issue, pp. 522-544
- Pattanaik, L.N. and Sharma, B.P., (2009). Implementation of Lean Manufacturing with Cellular Layout: A Case Study. The International Journal of Advanced Manufacturing Technology 42, pp. 773-778.
- Pavanskar .S.J., (2003). A classification scheme for lean manufacturing tools. Production and inventory management journal vol. 32 NO.3, pp. 6-10.
- M. and Shook.J., (1999). Learn to see value Stream Mapping to add value and eliminate muda. International Journal of Physical Distribution & Logistics Management, Vol. 30 No. 9, pp. 732-749.
- M., (2000). Application of lean principles to an enterprise value stream; a lean analysis of an automotive fuel system development process” International Journal of Production Research. Vol. 15 No. 6, pp. 555-565.
- Shah, R. and Ward, P.T., (2007). Defining the developing measure of lean production. Journal of Operation Management, pp 786-804.
- Shingo, S., (1988). Non-Stock Production, Productivity Press, Cambridge
- J.,(1990). “The machine that changed the World”. Rawson associates.
Get 3+ Free Dissertation Topics within 24 hours?